Tool shop offers high accuracy stainless steel turbine flow meters for sale, designed for media such as diesel, gas, kerosene, methanol and water, offering a wide range of aperture options from 1 inch to 3 inches and made of stainless steel or aluminum alloy as required to ensure long service life. The flowmeter is highly accurate with a tolerance of only ±1%, and can be used in a variety of industrial scenarios with an operating temperature range of -25℃ to +70℃.
Specification
Model |
T-K24 |
Applicable Media |
Diesel, Gas, Kerosene, Methanol, Water, etc. |
Nominal Diameter |
1 inch, 1.5 inch, 2 inch, 2.5 inch or 3 inch |
Material |
Stainless steel, Aluminum alloy (only 2.5 inch and 3 inch) |
Connection Method |
Thread |
Unit of Measurement |
QTS, PTS, L, GAL, m3 |
Measurement Accuracy |
±1% |
Maximum Working Pressure |
0.6Mpa |
Working Temperature |
-25℃~+70℃ |
Single Measurement Range |
9999 |
Cumulative Measurement Range |
29999999 |
Stainless Steel Turbine Flow Meter Dimension: (Unit: mm)
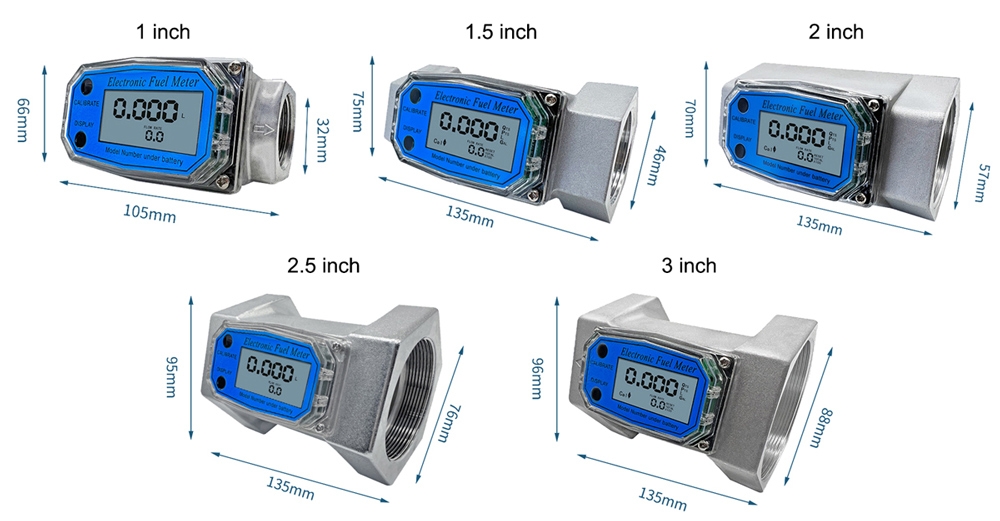
Stainless Steel Turbine Flow Meter Details
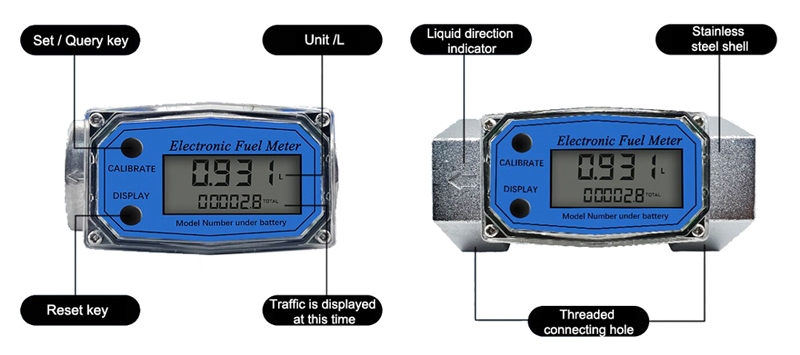
Stainless Steel Turbine Flow Meter Applications
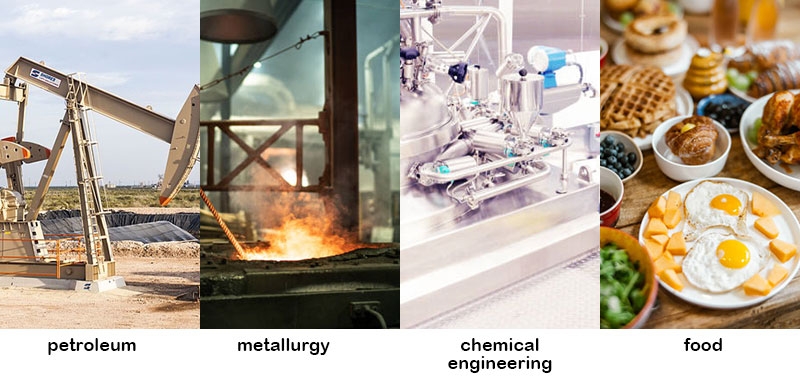
Tips: How do I maintain my stainless steel turbine flow meter to ensure accuracy?
The key to maintaining a stainless steel turbine flow meter is regular cleaning and inspection. Ensure that there are no excessive impurities or particles in the medium, these can cause the impeller to jam or wear out, which can affect measurement accuracy. Regularly check sensors and fittings for looseness and replace deteriorated parts based on frequency of use. If used in harsh environments, periodic calibration is also required to ensure accurate readings.